Oil and Gas
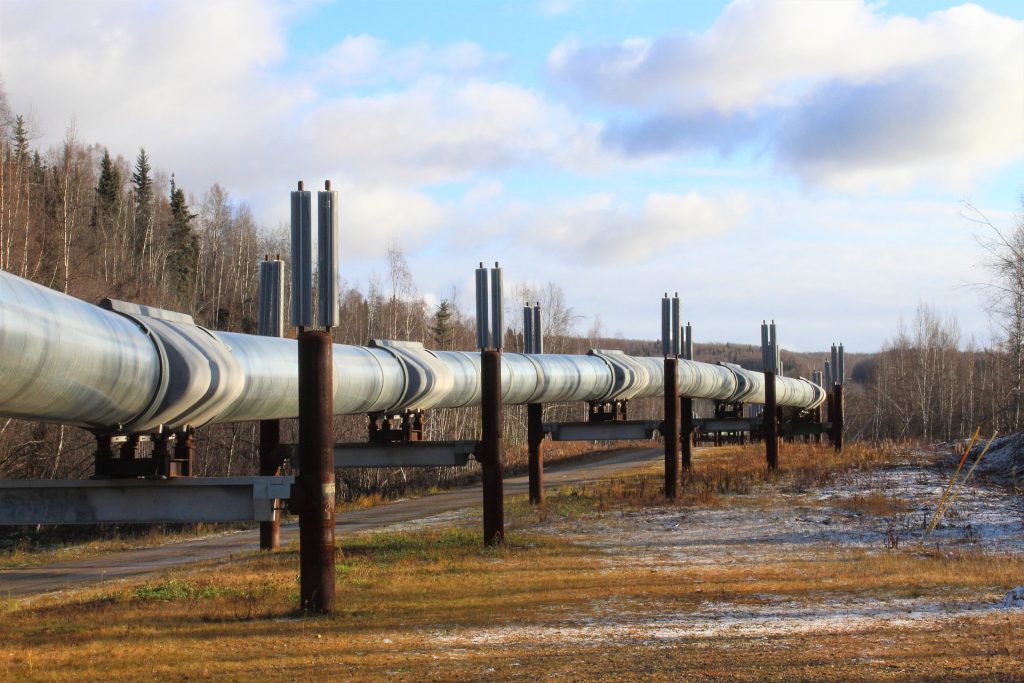
Quick Turnaround Time, Massive Data Collection, Tight Weather Window
Use Case: Implementing LiDAR in Pipeline Surveys Expands Project Scope Capabilities for MSI
Company: Measurement Sciences Inc.
Challenge
MSI, Inc. leverages lidar technology in the oil and gas industry by expanding their project scopes and increasing the number of completed surveys within the short fair-weather window between snowmelt to snowfall.
They implement lidar in pipeline surveys to be able to show a grander scope of the river crossing and banks. LiDAR enables their team to produce a much more detailed pipeline profile than traditional methods (i.e. taking gridded shots every 5 meters with GNSS), and offers expanded client deliverable offerings.
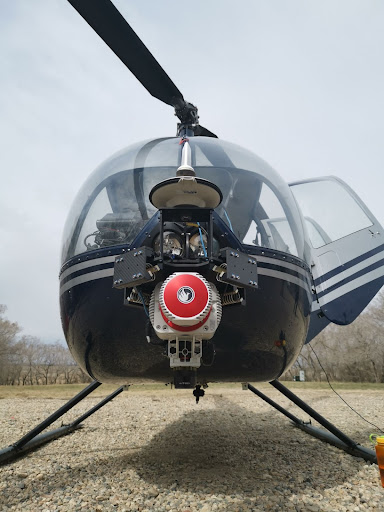
Solution
MSI, Inc. leverages lidar technology in the oil and gas industry by expanding their project scopes and increasing the number of completed surveys within the short fair-weather window between snowmelt to snowfall.
They implement LiDAR in pipeline surveys to be able to show a grander scope of the river crossing and banks. LiDAR enables their team to produce a much more detailed pipeline profile than traditional methods (i.e. taking gridded shots every 5 meters with GNSS), and offers expanded client deliverable offerings.
Application
MSI, Inc. leverages LiDAR technology in the oil and gas industry by expanding their project scopes and increasing the number of completed surveys within the short fair-weather window between snowmelt to snowfall.
They implement lidar in pipeline surveys to be able to show a grander scope of the river crossing and banks. LiDAR enables their team to produce a much more detailed pipeline profile than traditional methods (i.e. taking gridded shots every 5 meters with GNSS), and offers expanded client deliverable offerings.
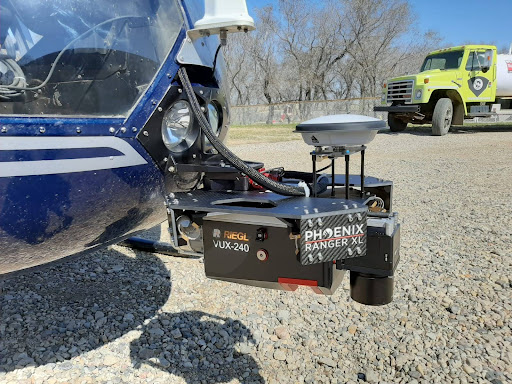
Results
MSI, Inc. owns and operates three Phoenix LiDAR systems: the MiniRANGER-1, RANGER-LR, and RANGER-XL. Their best collection windows are early spring and late fall, so they try to group as many sites together as possible to map consecutively during two sizeable RANGER-XL helicopter campaigns each year. They deploy the UAS-based miniRANGER to supplement sites between those two collection windows. This keeps the cost of helicopter operations down and still enables MSI to collect sites on demand, if needed, rather than waiting for the two seasonal windows. The decision process for which Phoenix system to deploy varies site by site – depending on time of year, project scope, and strictness of deliverable timelines.
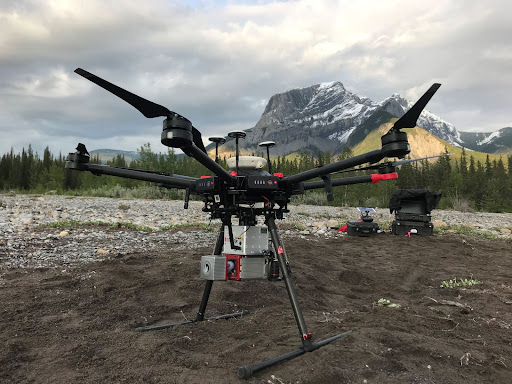
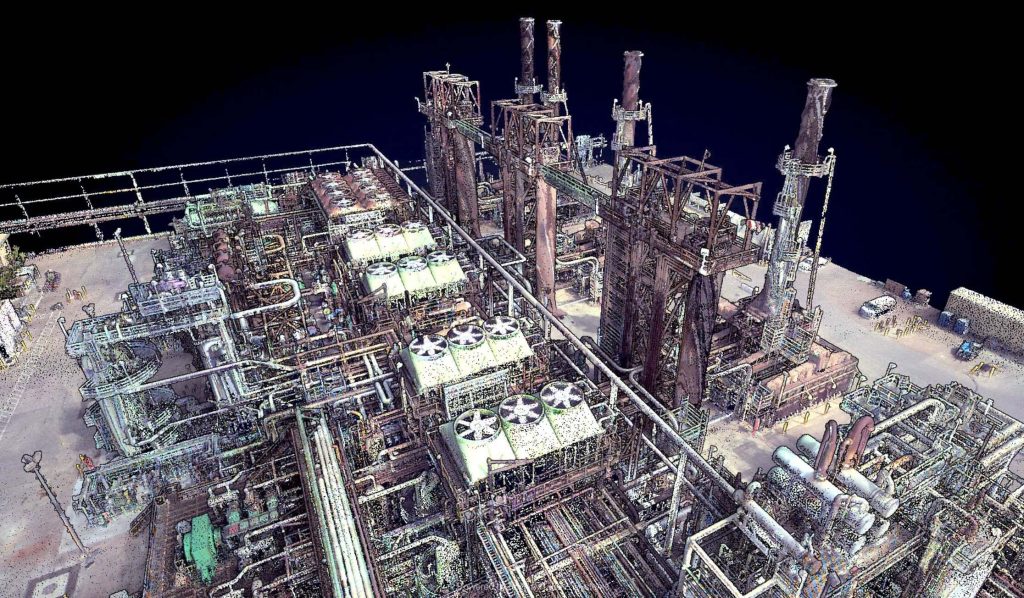
In this webinar, hosted by Kory Kellum of Phoenix LiDAR Systems, we explore the innovative use of LiDAR technology in oil and gas applications. Featuring insights from Ryan McMann and Andrew Healy of Measurement Sciences Inc. (MSI) and Scott McGowan of Precision Aerial Compliance Solutions, this session delves into the benefits of Phoenix’s survey-grade LiDAR mapping systems for UAVs and helicopters.
Learn how MSI transitioned from traditional land surveying to LiDAR, achieving efficient and detailed pipeline mapping and river-crossing surveys. Discover how Precision Aerial leverages LiDAR for refinery expansions, pipeline planning, and environmental assessments, significantly improving accuracy and efficiency. The discussion covers challenges in drone-based LiDAR surveys, data management strategies, and the integration of sonar and LiDAR for comprehensive results.
This video also explores potential applications in other industries, such as dam integrity and power line inspections. The webinar concludes with a Q&A session, addressing key questions about LiDAR technology’s capabilities and future developments. Don’t miss this insightful look at how LiDAR is revolutionizing the oil and gas industry.
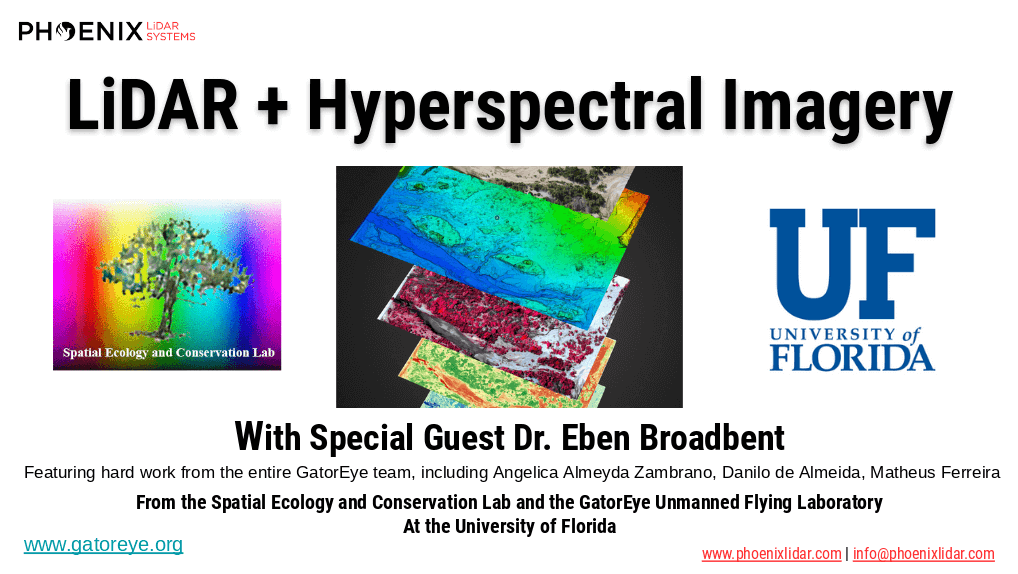
The high dimensionality of data generated by Unmanned Aerial Vehicle(UAV)-Lidar makes it difficult to use classical statistical techniques to design accurate predictive models from these data for conducting forest inventories. Machine learning techniques have the potential to solve this problem of modeling forest attributes from remotely sensed data. This work tests four different machine learning approaches – namely Support Vector Regression, Random Forest, Artificial Neural Networks, and Extreme Gradient Boosting – on high-density GatorEye UAV-Lidar point clouds for indirect estimation of individual tree dendrometric metrics (field-derived) such as diameter at breast height, total height, and timber volume.
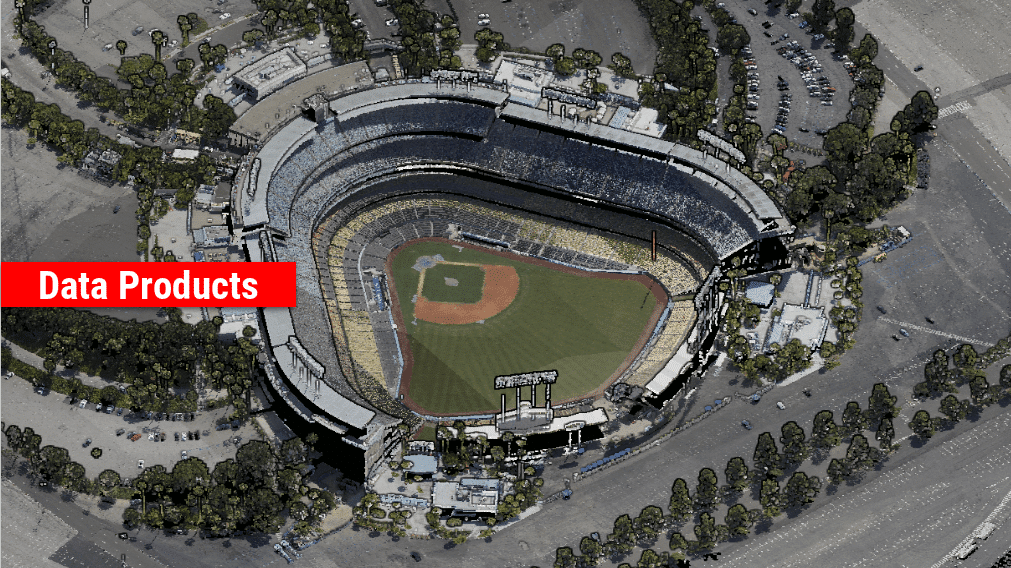
We’re excited to announce the release of LiDARMill v2! LiDARMill v2 takes automated post-processing to the next level. In our recent webinar, we covered some of the new improvements and features including:
- Imagery Processing in LiDARMill
- Ground Control Reporting and Adjustments
- Robust Coordinate System Handling
- A Workflow Overview and Demonstration
- Multi-Mission Processing Support
- Advanced Point Cloud Filtering Options
- RGB Thermal & Fusion
- Accuracy Reporting
- Automated LiDAR and Camera Calibration Options
- Near-Real Time (NRT) Reference Station Positioning for Projects Requiring Less Than 24 Hour Turn-around Time
- Trajectory Post-Processing Without Reference Stations
If you have any questions or would like to learn more about LiDARMill v2, please don’t hesitate to get in touch. We’d be happy to help!