Transportation
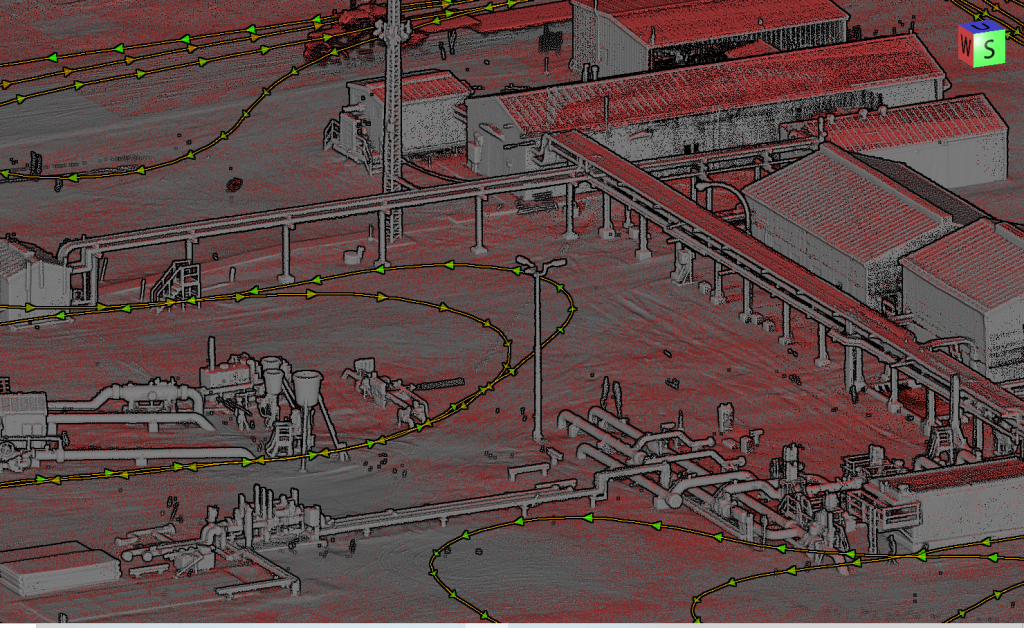
High Point Density, High Accuracy, Vehicle Adaptability
Use Case: Fusing Aerial and Mobile LiDAR Data
Company: Caltech Group
Challenge
Companies looking to perform large scale, high resolution mapping projects with budget restrictions and time constraints struggle using traditional surveying methods.
Caltech’s team of surveyors, engineers, CAD experts, technologists, and GIS specialists has spent the last 30+ years becoming Western Canada’s go-to company for geomatics services. Caltech provides services to many oil & gas utility clients. These clients demand some of the highest standards pertaining to data quality.
Caltech was contacted to generate a facility as-built of a site consisting of a myriad of pipes, buildings, and equipment. Using the mapping tools on hand, it would have been very difficult to complete the project, at least not to the level of accuracy that would be useful to the client. The only tool that could have been used was a terrestrial laser scanner, but due to the size of the facility – it was just not feasible.
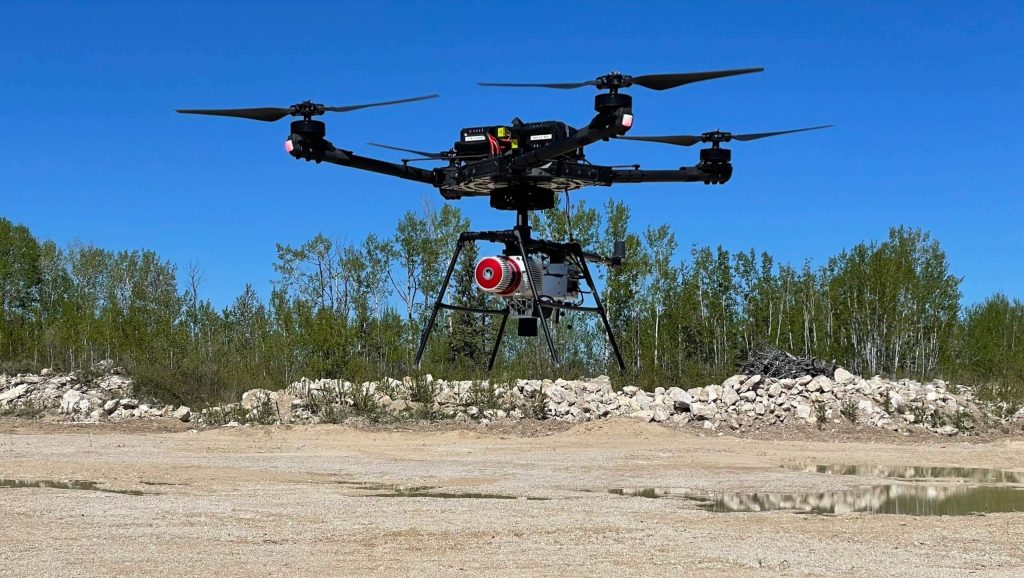
Solution
Caltech Group invested in a RANGER-LR mapping solution from Phoenix LiDAR Systems, allowing them to rapidly scan as-built facilities with high accuracy in a single day – the main motivator for acquiring a dual purpose UAS and terrestrial mapping system.
The derived data deliverables acted as a ‘digital twin’ of their clients’ facilities, empowering the end users to digitally visit their facilities and make informed decisions. The value-added ability to easily disseminate 3D geospatial data in a user-friendly format facilitated collaboration with people across all skill levels – both internally within their organizations and externally with subcontractors.
“The biggest advantage to purchasing the Phoenix Ranger LR system is its adaptability. It allowed our team to continue to offer UAS MMS services, but also to branch out into terrestrial MMS & helicopter-based MMS for larger area mapping & linear corridors.”
– Greg Stamnes, AScT, CMS – Geospatial Manager
Caltech Group
Acquisition
Step 1: Caltech accomplished the complex facility as-built mapping project by first mounting the RANGER-LR payload with 360-degree Ladybug camera to a truck and traversed through the site collecting 360-degree high-density lidar and spherical imagery.
Step 2: After the drive, they removed the payload from the truck, mounted the Sony A7R2 camera to it, and affixed the payload to an Alta X UAV, all without leaving the job site. This configuration enabled them to quickly collect aerial high-density lidar and imagery over the facility.
Step 3: The final step was to merge both the mobile and aerial pointclouds into a single cohesive dataset to be shared with the end user.
Results
Deploying the vehicle-adaptable RANGER-LR mapping solution allowed Caltech to successfully complete the data collection and turn around the deliverable facility as-built within a very short timeline. All project deliverables met or exceeded ASPRS accuracy specifications. The combination of rapid data collection, processing time, and data quality resulted in additional customer quotations for larger projects, subsequently awarded to the Caltech team.

Parameters
- Survey Area: 160-acre site
- Platform: Mobile Scan (truck) + Aerial Scan (Freefly Alta X)
- Site Features: Complex Pipe network, buildings, and equipment
- Time: 8 hours on site
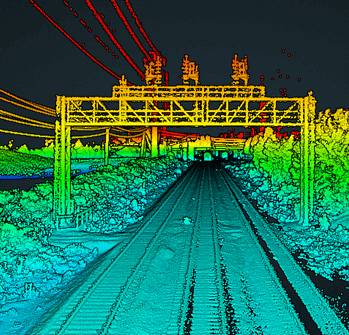
Application
The transportation side of CSX moves multi-million dollar equipment, from oversized generators to military equipment. To ensure the expensive cargo arrives safely to its destination, CSX first scans the planned route to extract cross-sections of bridges, tunnels, and other overhead obstructions from the LiDAR in order to identify clearance hazards prior to transport.
Results
CSX now owns and operates seven Phoenix LiDAR systems. (4) SCOUT-16 systems mounted on high-rail trucks with Ladybug cameras and (3) SCOUT-32 systems permanently installed on the backs of rolling rail cars. The high-rail trucks can travel on both road and railroad with this flexibility enabling them to go anywhere at any time to support immediate business requests. The rail-based geometry cars are designated to travel and cover the entire 21,000+ mile network at least one time per year as part of their safety protection protocol, with LiDAR continuously collecting data.
Parameters
Site: Rail Corridor
Solution: SCOUT-16 & SCOUT-32
AGL: 4 m
Ground Speed: 25-40 mph
Point Density: 800+ ppsm
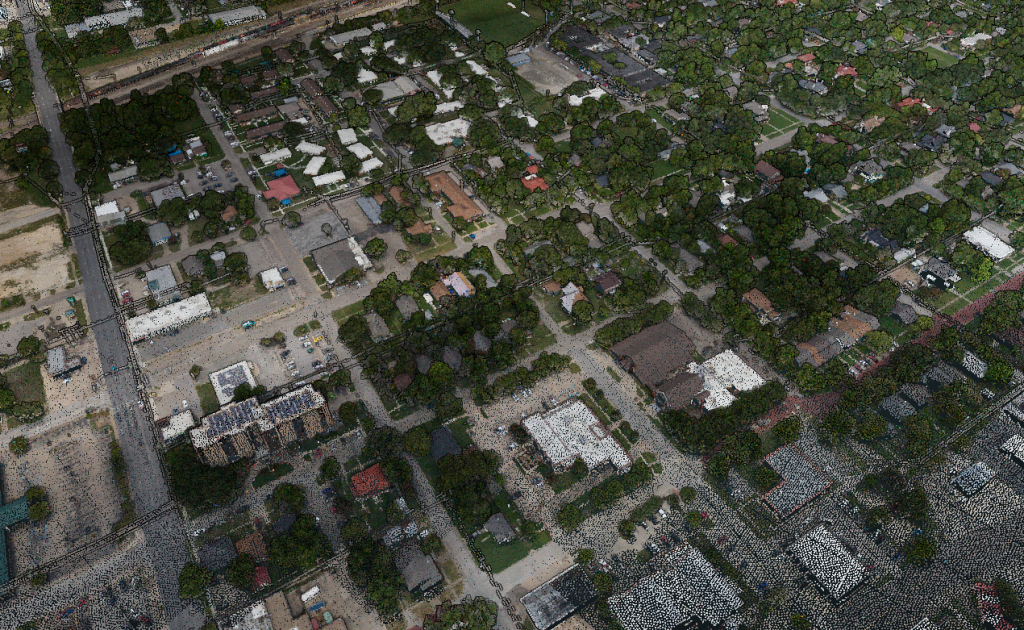
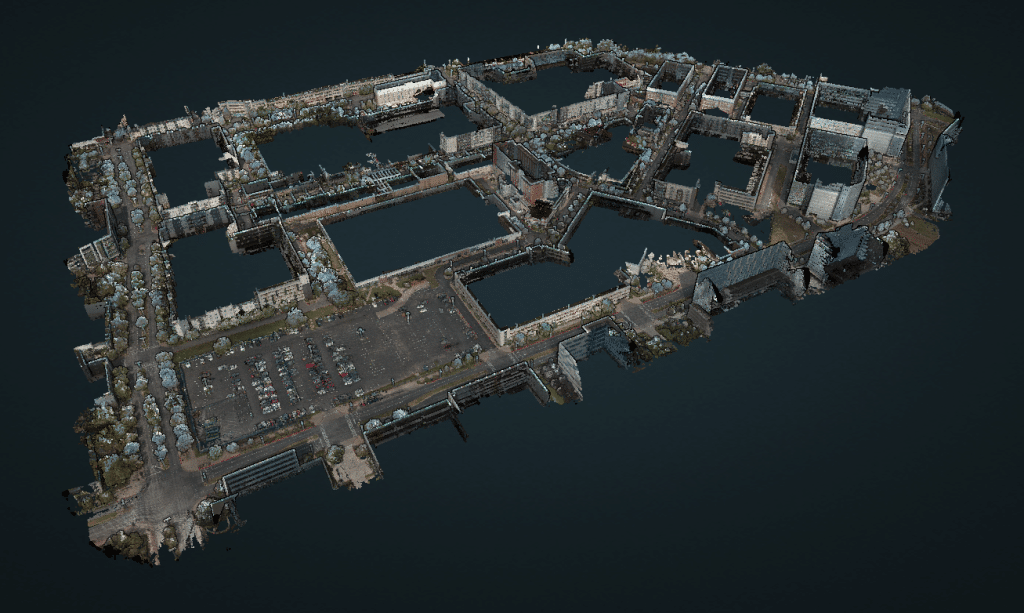
Speed: 20-30 mph
Point density: >2000 points/m²
AGL: Ground level
Acquisition time: 1.5 hrs
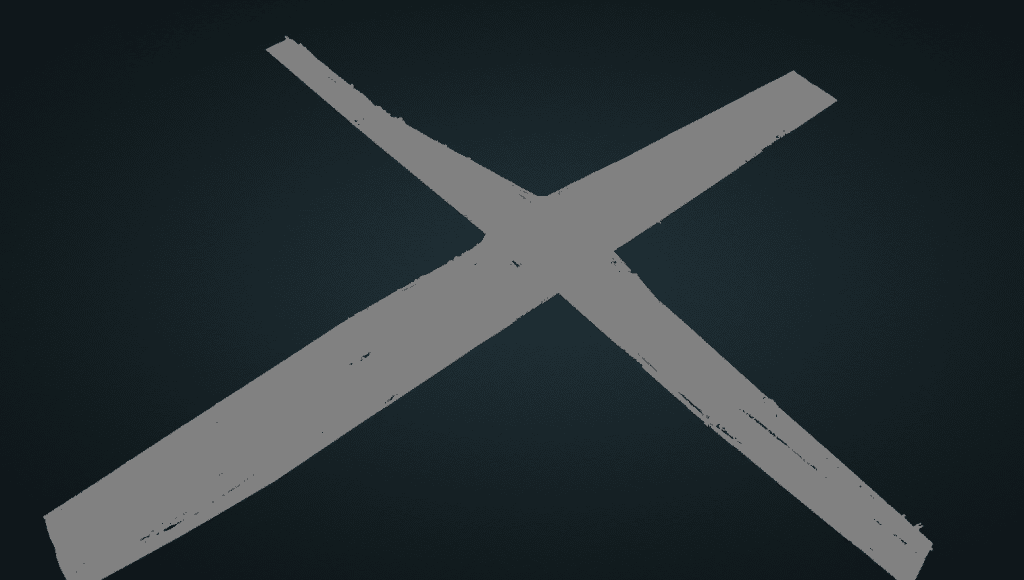
Speed: 40 – 60 mph
Point density: >2000 points/m²
AGL: Ground level
Acquisition time: 3.5 hrs
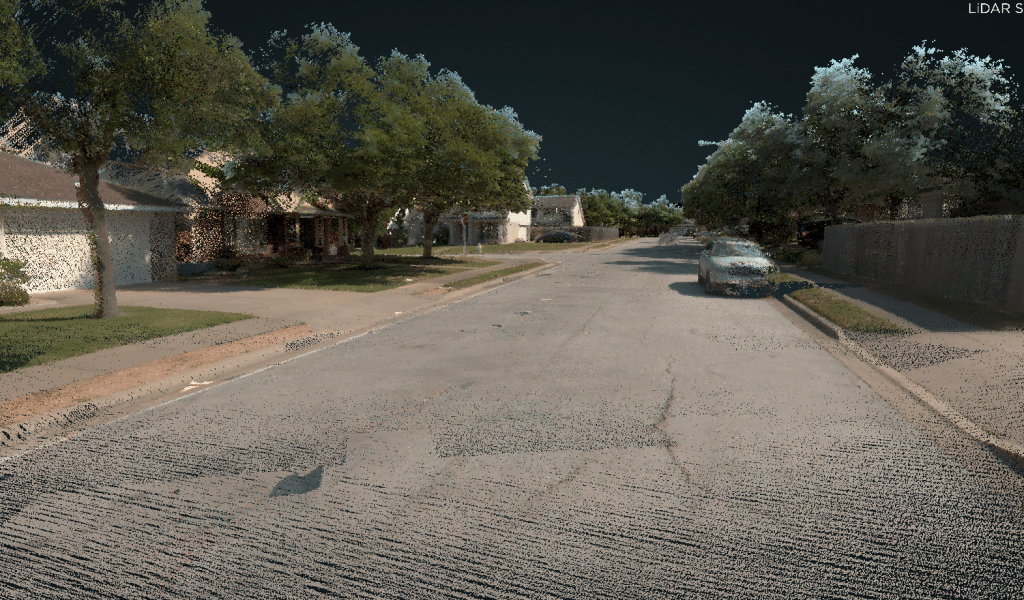
Speed: 20-40 mph
Point density: thousands of points/m²
AGL: Ground level
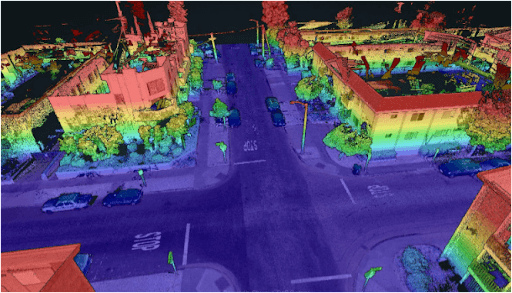
Point Density: 16,700 points per m^2
Height: ~1.5m AGL
Speed: Walking pace (~3-4 mph)
Data Acquisition Time: 12 minutes
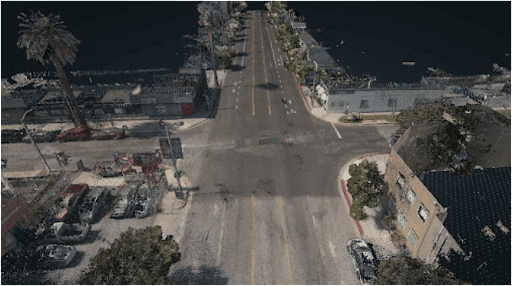
Point Density: 3920 points per m^2
Height: 2 m AGL
Speed: ~20 mph
Data Acquisition Time: 10 minutes